Planning for the Catastrophe
Practitioners often complain about the huge gap between practice and research related to the estimation of risks. In theory all is easy: A disruptive event just gets a probability and outcome assigned. But in practice these figures most often have to be estimated.
Todays article by Knemeyer et al. (2009) covers exactly this dilemma and tries to answer the question of how to plan for a catastrophe.
Catastrophes
A catastrophe can be defined as an event which happens with a low probability but comes with a large impact on the business.
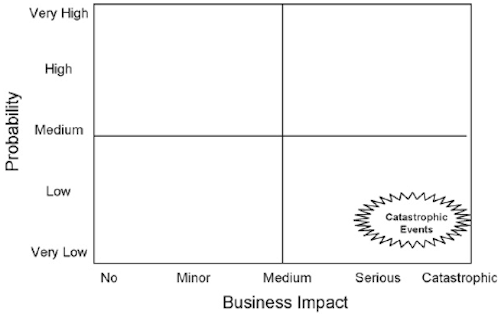
Estimating risks
Risk analysis is a major part of risk management. Figure 2 shows an example of a process where the data from a risk assessment is combined with the understanding of how risks are perceived by managers (e.g. read my articles on Managerial Risk Perception Part 1 and 2). Depending on the context managers seem to either over- or underestimate the probability of low-likelihood events, and since accuracy is very important (if you miss judge the probability of an 1% event by +1% you already doubled your probability and with it the expected loss)
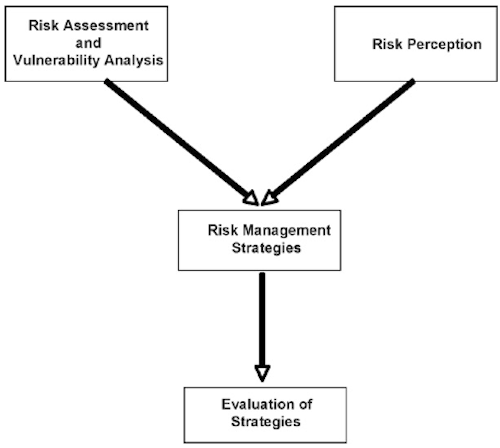
In the next step the strategies have to be devised and selected. Finally, the strategies should be evaluated on a regular basis to foster organizational learning.
Planning process
Figure 3 shows the suggested planning process.
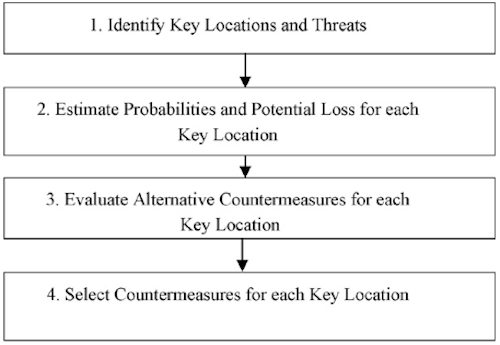
The first step in the planning process is to identify key supply chain locations. A location is considered key if interruption of its operations results in a major disruption in the flow of goods in the supply chain.
After finishing the first step, the manager should have a list of key locations, together with the major catastrophic events that should be considered.
As a next step the probabilities have to be estimated. The authors suggest catastrophe simulation as a tool to estimate probabilities. Figure 4 shows other possibilities. In addition to that, the potential losses have to be evaluated as well.
For the third step potential countermeasures are designed and selected in the next step for each key location. Figure 5 shows a sample of countermeasures and their impact on probability and incurred loss.
To select the strategies the authors suggest simple expected loss comparisons.
Conclusion
The suggested process should be suited for implementation within a company. Of course there are several simplifications which have to be analyzed prior to implementation. For instance, the authors suggest to use scenarios (each with probability and impact). I believe that when starting a process implementation like this it might be sufficient to use plain probabilities, but later on probability distributions make show a more detailed and accurate picture. But, I am wondering what you think? Could a process like this be used to improve the risk profile of a company?
Knemeyer, A., Zinn, W., & Eroglu, C. (2009). Proactive planning for catastrophic events in supply chains Journal of Operations Management, 27 (2), 141-153 DOI: 10.1016/j.jom.2008.06.002
Add new comment