Combination of Product and Supply Chain Design
In research the decisions on the product and the corresponding supply chain are usually separated. This happens for a variety of reasons, one may be the reduction of problem complexity, another that the research focus is on a brown field approach where the products are seen as given.
This makes this article even more interesting, since it combines the both decisions in one conceptual process and a model to optimize the decision.
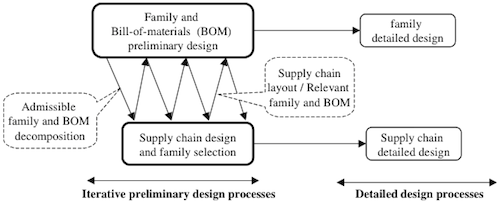
Process
The process (figure 1) consists of two major steps. First product variants are developed. In the second step a simultaneous optimization of the supply chain and the product variants is conducted.
The process is meant to be interactive, so that the product designer has the chance to make redesign decisions after step two to learn from the optimization results.
This leads to a generic Bill of Materials (BOM) which contains the different options for the product design alternatives.
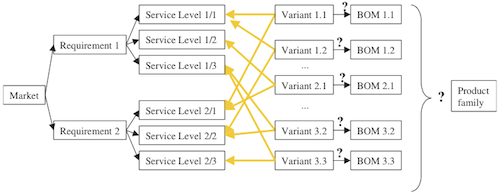
Model
The authors use a classic Global Supply Chain Model and extend it to consider the generic BOM. The objective is to minimize the total costs (addition of all fixed and variable costs), which is subject to the generic BOM and other constraints (e.g. capacity, shipping, …).
Application
Finally, the authors apply their model at a wiring harness supplier of a car manufacturer. Overall there are 48 possible product families. Using an implementation of their model the authors solve the supply chain optimization and conclude with the result in figure 2.
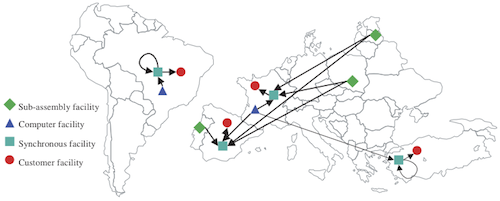
Conclusion
The idea of the generic Bill of Materials which contains all product variants makes it possible to integrate multiple product variants in the mixed integer linear program.
The algorithm seems to be fast enough to produce optimal solutions within minutes and can therefore be used as a basis for new models integrating other global aspects like taxes and exchange rates.
Lamothe, J., Hadjhamou, K., & Aldanondo, M. (2006). An optimization model for selecting a product family and designing its supply chain European Journal of Operational Research, 169 (3), 1030-1047 DOI: 10.1016/j.ejor.2005.02.007
Add new comment