Level of Detail in a Simulation Model
After the last more general entries on managers perception of risk and measuring SC performance I wanted to make a detour back to the basics.
Simulation is one of the tools, which can be used for analyzing supply chain dynamics, optimization and to support corporate decision making.
One major question when starting a supply chain model has always been what level of detail should you choose? Someone could start with a single worker in an agent based simulation model and continue with the machine he is operating, but when the goal is to gain insights about the interaction between your company and your closest competitors this might be too much information.
To get a better grasp on this topic I read “The impact of different levels of detail in manufacturing systems simulation models” by J.F. Persson (Translation).
Experiment / Results
To test the importance of the level of detail in a simulation model Persson designed an experiment: He modeled the same process chain with three different levels of detail:
- high level of detail
- some aggregation
- only main processes
After simulating this process and comparing the output measured in capacity utilization, inventory levels and blocked time (for bottleneck detection), he concluded that significant differences between the models have to be acknowledged (see figure).
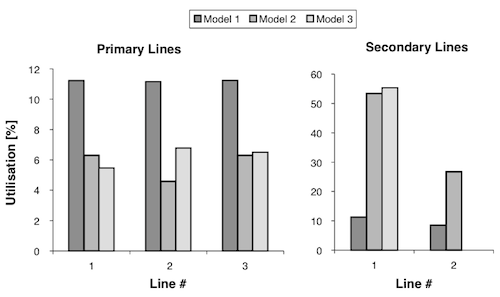
Conclusion
So what are the important lessons for someone planning to develop and use a supply chain model:
- Focus
Know your exact goals and focus on achieving them. If you want to analyze competitive interaction between companies, it might be a good idea to have a single company as your base entity - Minimization
The level of detail should be kept at a minimum, keeping the model simple. The reason is that (i) a simple model can provide a result and (ii) an unimportant detail in the model is hard to remove despite the negative impacts on simulation execution time.
- Validation
It is very important to have constant validation for the model during the development process and final approval tests to prevent adverse effects from a wrong level of detail as well as other mistakes.
Persson, J. F. (2002). The impact of different levels of detail in manufacturing systems simulation models Robotics and Computer-Integrated Manufacturing, 18 (3-4), 319-325 DOI: 10.1016/S0736-5845(02)00024-8
Add new comment