Optimal Design of Supply Chain Networks with uncertain Demand
This week is dedicated to the works on supply chain management from Greek supply chain researchers. Today’s article has been published in the Journal of Management Sciences (Omega) by four researchers from northern Greece and the UK.
After my last reviews which focused more on the conceptual aspects of supply chain risk and management. This paper is again more hands-on in the sense that it describes a mathematical model which integrates supply chain design and uncertain demand and therefore leads to a more robust supply chain design.
Method
The authors propose a mixed-integer linear program to solve a strategic supply chain design problem. Strategic design decisions include:
- Where to locate new facilities (be they production, storage, logistics, etc.).
- Significant changes to existing facilities, e.g. expansion, contraction or closure.
- Sourcing decisions – what suppliers and supply base to use for each facility.
- Allocation decisions – e.g., what products should be produced at each production facility; which markets should be served by which warehouses, etc.
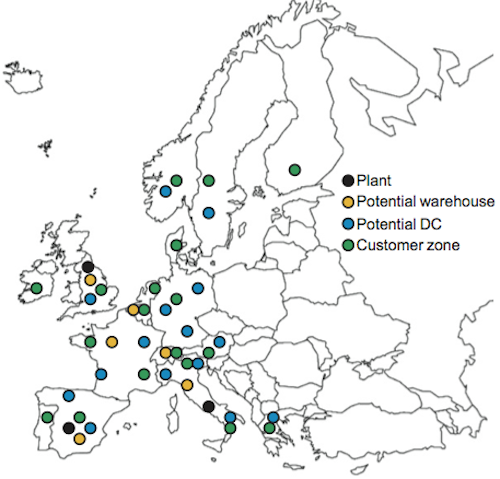
Model parameters
To be useful supply chain models usually are limited to a specific supply chain context. In this case the goal is to select an optimal design as well as some tactical / operational parameters.
Figure 1 and 2 describe the location design aspects of the model. The locations of plants and customers are fixed; for the warehouses and distribution centers a set of possible locations is given, and the optimal location has to be selected from the sets.
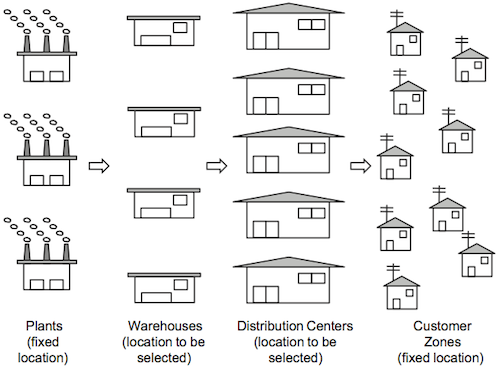
There are several more constraints implemented, which are concerned with the transportation flows, production resources, safety stocks and capacities. Inventory can be held at different locations, which is solved during the optimization of the model.
The objective is to minimize expected total cost over the planning horizon.
Uncertainty
There are two basic options to integrate uncertainty into a mathematical model:
- scenario approach, which discretize the uncertain parameters into a limited number of specified scenarios, or a
- probabilistic approach, using stochastic programming.
The authors select the first approach:
In this paper, we adopt a scenario planning approach for handling the uncertainty in time varying product demands. A question that needs to be addressed in this context concerns the generation of the scenarios to be considered. It is, of course, possible to assume that the demand for each product in each customer zone is an independent random parameter. However, more realistically, demands for similar products will tend to be correlated and will ultimately be controlled by a small number of major factors such as economic growth, political stability, competitor actions, and so on.
The complexity of the overall-model is then dependent on the complexity of the basic model (e.g. number of possible connections and locations) and the number of selected scenarios.
Two kind of decisions must be considered in the model: here-and-now decisions (the “really strategic ones”), those have to be selected before any more knowledge about the outcome of the uncertainty can be obtained. The wait-and-see decisions are those which can be altered during a model run. The concept is shown in figure 3.
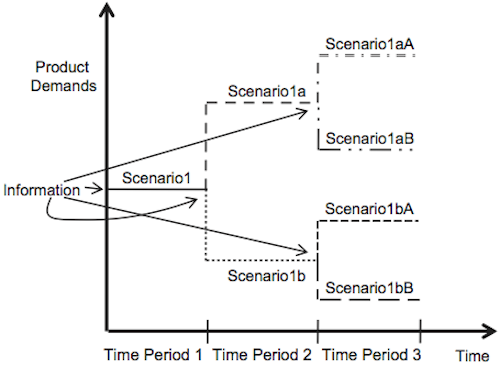
Case study
The authors then set the parameters for the model using an “European wide production and distribution network comprising of three manufacturing plants producing 14 different types of products and located in three different European countries, namely the UK, Spain and Italy” (see figure 1).
The proposed demand volume is given in four scenarios for all customer areas and products. Two cases are compared: one with low safety stock and another one with a general higher safety stock level.
The resulting optimal supply configuration for the high inventory case is shown in figure 4.
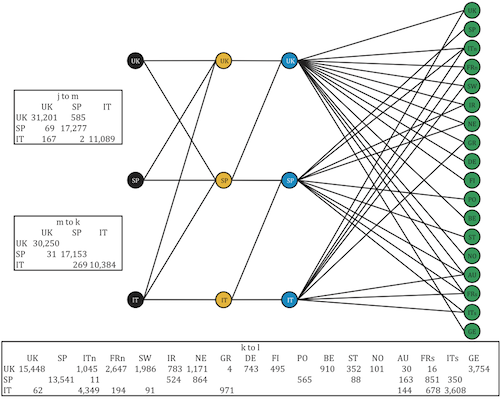
Conclusion
The authors keep up to their promise and delivered a quite detailed model description and its results. But still, would it be possible to reproduce their results or rebuild their model using this data only? Very unlikely.
Even though the model is detailed. There is still a lot of information missing about the specific parameters used and the interconnections in the model. One major factor in the scientific acceptance and validity of research is the reproducibility of the results. And sadly, that’s one of the reasons, why complex models are still not commonly presented in renowned journals.
In my opinion the only chance to circumvent this obstacle is not only to publish the article, but also the complete model source code and the parameters used.
In the article these omissions are necessary to stay below a certain page limit – the authors already had to distribute the result charts of their case study throughout the paper to have a chance to include the most relevant ones.
But beside these necessary exclusions, I found that some other things would have been interesting to read about.
- Demand risk: For a strategic (i.e. long term) model and so many different demand centers, I think only four demand scenarios might be too few to represent reality in a sufficient way. More scenarios could have been included, since the CPU time it took to calculate one optimal solution was quite low (some hundred seconds only).
- Other risks: Furthermore it would have been interesting to analyze the effects of other risks in the model, but they were omitted as well.
- Overview: I was also missing a short general overview over the given scenarios.
- Sensitivity analysis: Lastly, the validity of a model can be further improved by analyzing the sensitivity of the model towards parameter change. The authors did not omit this point, but they choose to test and present only two deviations from their original model parameters, which I think is too little to assess the validity of the model sufficiently.
I think my conclusion can be summarized as follows: It is definitely hard to present a complex supply chain model in a way which sustains the validity and reproducibility of the results. But, since the description of the model is quite elaborate, this paper can still be a great source and foundation for one’s own strategic supply chain model.
Georgiadis, M.C., Tsiakis, P., Longinidis, P., & Sofioglou, M.K. (2011). Optimal design of supply chain networks under uncertain transient demand variations Omega, 39 (3), 254-272
Add new comment