Exception Handling for Robust Supply Chain Design
This article considers the design of robust supply chains from the viewpoint of exception handling. Disruptions of the supply chain happen all the time. Smaller disruptions like quality issues are part of the daily business; but a look at the recent ten years shows that large disruptions, happen more often as well (think of terrorist attacks or earthquakes). “Thus, exception management is an important issue in global supply chain networks.”
Basics and definition
If one accepts the fact, that exception cannot be eliminated completely there are two ways to treat them: preventive and interceptive. Figure 1 shows different exception management strategies.
The authors define a supply chain exception as the opposite to the classical seven-Rs of logistics:
We can use this description to define a supply chain failure or exception occurring whenever the supply chain deviates from any one of the […] required specifications – either in terms of delivering the wrong product, in the wrong quantity, in the wrong condition, at the wrong place, at the wrong time, at the wrong cost and to the wrong customer.
Exception management
In this case exception management is addressed “at the strategic level through the preventive selection of supply chain partners that mitigate risk in the network.”
In the first step the consequences of a given exception (here: supplier non-performance) are analyzed. The authors use a Cause-Consequence-Diagram for this end (figure 2).
Then, “given the probability of occurrence of the initiating event, which is supplier non-performance, and the probabilities for the various intermedialy events, we can calculate the probability of occurrences for each of the end states or outcomes. Furthermore, each of these end states may result in different levels of supply shortfalls and financial cost. Hence, given the probability of each end state and the supply shortfall or financial cost for each end state, we can calculate the expected shortfall or financial risk for the non-performance of a given supplier.”
If repeated for each supplier, the supplier with the least expected impact can be identified.
Model
To implement their approach the authors develop a small linear mixed-integer model.
The model was formulated in Microsoft Excel and solved using the Solver add-in. The model was solved for a problem with a single manufacturer (located in the US), dealing with 5 suppliers. The probabilities of supplier disruption for all the suppliers (individually and in various combination) were considered as given [the first part is shown in figure 3]. The relation cost was taken as $5000 and the quantity required by the manufacturer was 520 units.
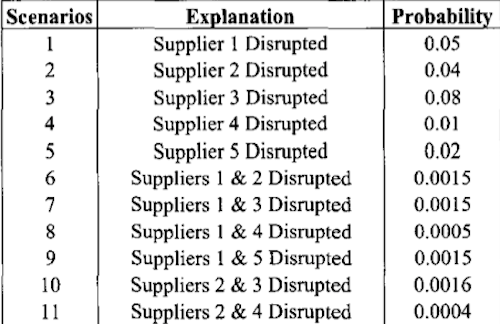
Conclusion
The presented approach makes it easy to include uncertainty into the supplier selection process. Considering the moderate efforts necessary for implementing the supplier assessment and implementing the model, I would like to read more about the effectiveness in a real business situation.
Gaonkar, R., & Viswanadham, N. (2003). Robust Supply Chain Design: a Strategic Approach for Exception Handling Proceeings of the 2003 IEEE International Conference on Robotics & Automation, 1762-1767
Add new comment