Predicting and Managing Supply Chain Risks
I often recommend Supply Chain Risk: A Handbook of Assessment, Management, and Performance as a good overview of supply chain risk management literature. In this article I summarize chapter four of the book on the problem and processes to predict supply chain risks.
Structure and basics
In first section the author starts by defining the basics of risk and uncertainty. The next section briefly introduces different categories for supply chain risks:
- Internal to the firm: Process, Control
- External to the firm but Internal to the Supply network: Demand, Supply
- External to the network: Environmental
These risk can then impact the different dimensions of a supply chain:
- Physical movement of goods
- Flow of information
- Flow of money
- Security of the firm’s internal information systems
- Relationship between supply chain partners
- Corporate social responsibility and the effect on a firm’s reputation.
The next section provides an overview on supply chain risk management, its steps and mitigation strategies.
Predicting Supply Chain Risks
One of the main requirements for an effective proactive risk management process is to obtain good estimates of the probability of the occurrence of any particular disruption and accurately measure the potential impact.
So the estimation of probabilities and impacts, depending on the characteristics of the supply chain and the environment it might be harder to identify all risks and assess them.
The author describes two tools for the estimation of risks: Data Mining and Failure Mode Effect Analysis (FMEA).
Data Mining
The role of data mining is to analyse historical data, to improve prediction capability. Some of the common analytic approaches used by data miners are:
- Estimation of the parameters of past performance: Means, Standard deviations, Correlations, and Associations for hypothesis testing
- Classification: Segmentation, or Clustering of data units to facilitate the modelling process
- Construction of a functional relationship: or model between responses and explanatory variables.
The following tools should be used by a data miner:
- Estimation: […] These tools will not lead to patterns but are more useful in analysing the data to identify the most relevant sets of data to concentrate further analysis.
- Clustering/segmentation: This approach is used to logically group observations on the basis of similarity in their characteristics, reducing the level of heterogeneity in the data.
- Classification/discrimination: The process of assigning observations to a predetermined number of classes.
- Prediction: Formal mathematical models are built for the purpose of predicting the occurrence of the phenomenon.
Failure Mode Effect Analysis (FMEA)
The goal of the FMEA is to
- Recognise and evaluate the potential failures of a product or process and the effects of that failure.
- Identify actions, which could eliminate or reduce the chance of the potential failure occurring.
- Document the entire process.
The author highlights ten steps of the process:
- Define scope, functional requirements, design parameters and process steps.
- Identify potential failure modes: Failure modes indicate the loss of at least one functional requirement. It is the manner in which a failure occurs. This step in the process takes into account a foresight view (based on past experience and any new information) of what could cause a failure to the system or process.
- Potential failure effect: This step investigates the effect the failure will have on other entities or processes.
- Severity: “How bad” or “serious” the effect of the failure mode is. Usually severity is rated on a discrete scale from 1 (no effect) to 10 (hazardous effect). Severity ratings of 9 and 10 indicate a potential effect of high importance and this could typically be a safety or government regulation issue. Critical effects need deeper study for all causes to the lowest level, using a method of Fault Tree Analysis.
- Potential causes: These are the causes of the failure. In this step, all causes that can be attributed to the failure occurring are investigated.
- Occurrence:This is the likelihood of the event happening (i.e. failure in the system) on the basis that “the cause occurs”. FMEA assumes that if the cause occurs, failure will occur too. The probability of occurrence is ranked from 1 to 10, where 1 signifies a remote probability of occurrence and 10 a very high probability of occurrence.
- Current controls: The objective of the controls is to identify and detect the deficiencies and vulnerabilities as early as possible. This step looks at the current processes in place to mitigate the failures (if already known).
- Detection: A subjective rating is assessed corresponding to the likelihood that the detection method will detect the first-level failure of a potential failure mode. This is ranked from 1 to 10, where 1 signifies that it is unlikely to detect and 10 signifies a very high detection potential.
- Risk Priority Number (RPN): These are used to prioritise the potential failures and are calculated as “Severity Occurrence Detection ranking”.
- Actions Recommended: The team should then select and manage subsequent actions needed to locate and control the situation.
Predictive – Proactive Methodology
Based on these methods the author suggests a predictive-proactive methodology (figure 1) to manage risks.
The two main steps are called predictive mode and proactive mode. In the predictive mode, the focus is on gathering of information on the potential risk sources. The proactive mode focusses on the identification of the risks within the supply chain and assessing the risk level and setting the strategic objectives of the company.
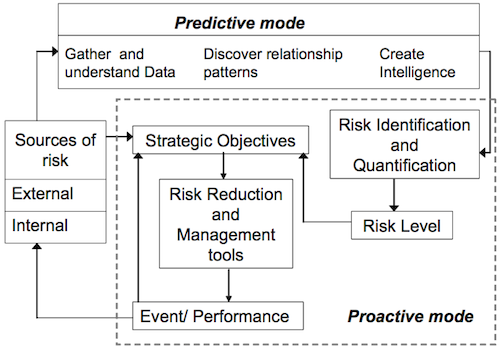
Conclusion
I read the chapter with a focus on the description of the prediction tools. The model on the other hand is a nice add-on which could be used as food for thought. But I find it a little bit too simplistic and a little bit confusing. It describes a basically linear process (from a risk to the disruption), but why then did the author choose not to represent this in a linear way, but in a diagram with two main parts/frames instead of a clear process and why are there two different types of frames (dashed and solid)?
Dani, S. (2006). Predicting and Managing Supply Chain Risks Supply Chain Risk (Ed. Clare Brindley), 53-66 DOI: 10.1007/978-0-387-79934-6_4
Add new comment