Relative Improvements of Supply Chain Redesign Strategies
The Bullwhip Effect was first discovered and analyzed in the 1950s. It triggered more intense research on the supply chain system (even though the term supply chain was not yet coined).
Starting in the early 1980s, this research finally lead to significant changes in real supply chains as well.
This article does a follow up on these developments and evaluates the relative improvements of each of the strategic stages.
Supply chain redesign process
The authors refer to a supply chain redesign process called “Cardiff methodology”. It is depicted in figure 1, key elements are the real supply chain as a starting point, this supply chain is then analyzed and converted into a conceptual model of the chain. In the the next step this conceptual model is transformed into a mathematical representation and then simulated to generate new insights on the dynamic behavior of the system. Lastly, this knowledge is used to adapt the real supply chain, and the process is restarted.
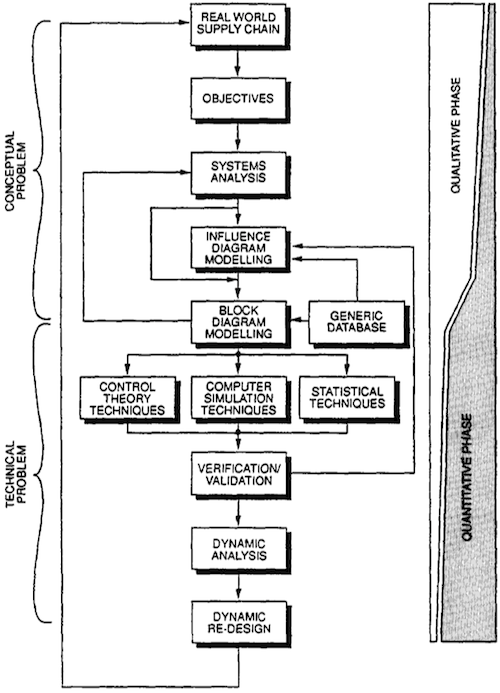
History of supply chain redesigns
The article in great length on the shifting redesign paradigms since the 1980s. Four phases are distinguished here. I will highlight the corner stones of each of them.
- Phase 1 – Just in time
Just in time initiatives were launched in the early 1980s, with the goal of reducing in-plant lead times. As a result: “The application of JIT techniques have achieved very significant reductions in lead-times and inventory. In European plants, the average manufacturing cycle time from component start to finished good shipment has been reduced by around 50%, with an accompanying drop in inventory.” - Phase 2 – Interplant planning and logistics integration
The next step was to improve the information flows thoughout within the company and on its edges. Key components here was the introduction of MRP systems and the supporting EDI. - Phase 3 – Vendor Integration
During the next phase the focus shifted towards the supply side. And the vendors were integrated into the systems established in Phase 2. - Phase 4 – Time based management
Should be seen as a broader view on the above mentioned steps to lead time reduction. So time based management includes the comprehensive reduction of total cycle times from product development to the end customer.
Case study
The author use a case study to highlight the effects of above mentioned strategies on supply chain performance. Using the example of a PC supply chain the authors create a computer simulation model of this specific chain and test the above mentioned redesign strategies. Overall five different models are generated one baseline case including the state of the supply chain before the redesign strategies and one model for each of the four phases mentioned above.
The results can best be seen in figure 2.
At about time 5 a positive demand shock is induced into the system, after that customer demand is constant again. The results show decreasing factory order rate fluctuations with each new strategy employed.
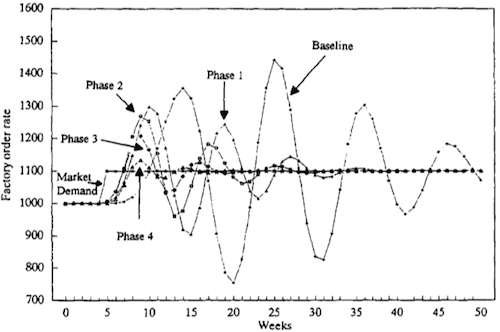
Conclusion
This article has two major contributions first it has a very informative listing of the strategic paradigms during a 20 year time period. Furthermore it also shows that these strategic changes have not been in vain, but each of the phases has the potential to improve the supply chain performance.
Berry, D., & Naim, M. (1996). Quantifying the relative improvements of redesign strategies in a P.C. supply chain International Journal of Production Economics, 46-47, 181-196 DOI: 10.1016/0925-5273(95)00181-6
Add new comment